drop test simulation time|numerical drop test : wholesale Below are the steps to complete a successful drop test analysis in SOLIDWORKS Simulation. 1. Apply Materials . Linear-elastic or elastoplastic material can be defined for the drop test. For most simulation studies in .
Please select an Army unit from the dropdown below or go to the branch page. Branch Page. ARMY. NAVY. MARINES. AIR FORCE. COAST GUARD. JOINT. CIVILIAN.
{plog:ftitle_list}
Resultado da Welcome to AZLyrics! It's a place where all searches end! We have a large, legal, every day growing universe of lyrics where stars of all genres and .
Software that can simulate a drop test experiment accurately yields dramatic cost and time-to-market benefits for manufacturers. Altair drop test simulation is applied in various industries including electronic devices, cell phones, household appliances, white goods, and packaging.
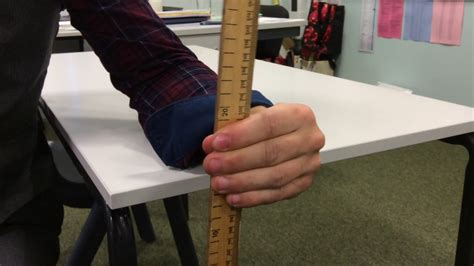
Software that can simulate a drop test experiment accurately yields dramatic .
Software that can simulate a drop test experiment accurately yields dramatic cost and time-to-market benefits for manufacturers. Altair drop test simulation is applied in various industries .
Today, we're going to talk about how to perform a drop test in LS-Dyna. Why do we do drop tests? The main reason is to evaluate how well the product design and the material will perform when exposed to the amount of external impact .
Users will need to consider many factors: materials, meshing, performance, runtime, and more. In this paper, we will discuss five best practices and key features for drop test simulation using .
Below are the steps to complete a successful drop test analysis in SOLIDWORKS Simulation. 1. Apply Materials . Linear-elastic or elastoplastic material can be defined for the drop test. For most simulation studies in .The first time performing a SOLIDWORKS Simulation Drop Test study is typically a little slow to load as the steps are being rendered. Afterward, however, it will run smoothly. An animation of the Stress results shows how stresses .A drop test simulation typically takes hours Of computing time. If you make a mistake, it will waste Of time. As a good practice, always perform the simulation incrunentally. In this case, .Impact analysis, also known as drop testing, is one of the most important stages of product design and development. Software that can simulate a drop test experiment accurately yields .
Drop test simulation tools allow Modeling and Simulation engineers to quickly predict product drop performance and modify the design to meet the specified use criteria.An experimental drop test may be already too late to correct the actual design. That's the reason why this simulation of our drop test plays a critical role. As we see here, the drop test workflow can be separated into three major parts . Drop Tests are a kind of study in SOLIDWORKS Simulation Professional and Premium that simulates dropping a model on the ground. Simulation drop Tests are the only type of study in SOLIDWORKS .
Westpak offers white papers as a useful time-saving reference. Leadership & Principles. . This type of simulation is designed to mimic both potential mishandlings and expected circumstances a product and its packaging may . Its drop test simulation software accurately reproduces reality, offering considerable control over various contact conditions. This proves beneficial for manufacturers as the various stages of product testing occur within a digital environment, allowing for significant time and money to be saved during development.Create the model for this simulation with ABAQUS/CAE. A Python script is provided in “Circuit board drop test,” Section A.13. When this script is run through ABAQUS/CAE, it creates the complete analysis model for this problem. Run this script if you encounter difficulties following the instructions given below or if you wish to check your work.We highly recommend you review the course details which include the course overview, learning outcomes, prerequisites, and the total time time required to complete the course, before you complete the purchase of this premium learning course on Drop Test Simulation Using Ansys Workbench LS-DYNA. Time duration: 180 days after the purchase
Lets you specify the directory to store the simulation results folder. . A nonlinear solution takes more time and resources than a linear solution but gives more accurate solution. Large displacement formulation is used by default. . In the Drop Test dialog box, you can: Clear the Large displacement option to specify a linear solution .
Perspiration Color Fastness Tester mfg
Integrative tool chain with considering fiber distribution from process simulation to explicit structural simulation is implemented for an ECU level drop simulation, with which consistent ECU level drop tests are performed. By means of comparing critical drop height acquired from test, the feasibility of this tool chain simulation is shown.
To carry out bus rollover simulation with compliance with ECE R66 regulation. Based on ECE R66 Regulation, Simulation is one of the accepted methods to carry out Rollover assessment. Simulation appears to be a better option, as it is cheaper in terms of cost, faster in time, comparing to physical tests. 3. They requested drop test to drop 10 times. 4. QA counted “FAIL” due to with deformed of cartons and packed of boxes at corner placement. 5. QA asked to no need re-do the drop test and file this for QA master file already. Reply
numerical drop test
The first time performing a SOLIDWORKS Simulation Drop Test study is typically a little slow to load as the steps are being rendered. Afterward, however, it will run smoothly. An animation of the Stress results shows how stresses spread through your model over time from the impact point. In a drop test analysis, we typically have two main components: a moving test specimen (which can be a single body or an assembly) and the fixed ‘ground’ body. . Simulation Time Steps. The integration time step for the impact analysis must be small enough to properly capture the movement, peak stress, and physical contact development. . The solder joints drop reliability is a significant concern for handheld electronic products. This chapter presented two major drop test modeling methodologies for the solder joint drop test reliability. One is the controlled pulse drop at board level modeling and simulation and the other is the free fall board level drop test.
Drop Test Simulation for Designers. In the past – in order to perform a finite element simulation – an expert analyst would have to manually walk through the steps of finding and cleaning up the geometry, seed and . In this solidworks tutorial, we will briefly go over how to simulate a drop test! Very important for predicting part impact so you can improve your designs#.Drop Test Simulation Using Ansys Workbench LS-DYNA (Self-paced Learning Available) Course Overview. Drop testing is one of the most important stages of design and development of many products. Engineers conduct drop tests in a controlled setting in different orientations to evaluate if their designed product can withstand drop impacts. With . The solder joints drop reliability is a significant concern for handheld electronic products. This chapter presented two major drop test modeling methodologies for the solder joint drop test reliability. One is the controlled pulse drop at board level modeling and simulation and the other is the free fall board level drop test.
However, since the drop test is a time-wasting method, the simulation technique is necessary to shorten the design stage and get the optimized solution. In current study, LS-DANA was used to do . This is a short overview of how to use the Drop Test capability in SOLIDWORKS Simulation to approximate real-world impact tests on consumer products designed.Create a drop test study. Right-click the top icon in the Simulation study tree and select Study to access the Study dialog. Define the Properties of the study to select a small or large displacement formulation. . Running a drop test study can take a long period of time due to intense computations. View results: Double-click an icon in a .
SOLIDWORKS Simulation uses an Explicit method for solving Drop test analysis and despite the fact that solving Drop test involves capturing results within microseconds of impacts with thousands of small-time steps, with SOLIDWORKS, it’s quick and simple for users to set up and study drop test performance of designs.Lets you specify the directory to store the simulation results folder. . A nonlinear solution takes more time and resources than a linear solution but gives more accurate solution. Large displacement formulation is used by default. . In the Drop Test dialog box, you can: Clear the Large displacement option to specify a linear solution .Figure 6. Drop height. Table 2. Drop-test parameters and their values Drop-test parameter Drop height (h) Gravity (g) Plot step number (ns ) Solution time after impact (ti ) Value 237 mm 9.81 m s−2 25 2000 µs CONCLUSIONS Deformation behaviour simulation on dropping a sample cherry tomato has been discussed in detail in this paper.
market competition. This study concerns both simulation and physical test for drop impact. This test carrier is a top housing of a Motorola CD938 cellular phone attached with aluminum plate on four boss locations so that overall weight is equal to the weight of a real CD938. A drop test platform developed and patented by Chen, et al. [7-8] was . Hello everybody, I am trying to simulate a drop test of a headform & helmet in ProMechanica. I have actual acceleration and time readings from the accelerometers and material properties required for modeling the components however I wanted to know how should I proceed in simulating this concept. S. This enables the software to account for energy lost in the dynamic simulation. This is in contrast to a linear elastic material that would bounce at the same magnitude repeatedly. 2. Drop Test Setup. A height or impact velocity can be chosen for the drop test. Gravity is also defined. The choice of parameters here is dependent on your test .
drop test simulator
drop test simulation software
Salmos 14.5 – 7: Deus entre os justos. 5 Olhem! Estão tomados de pavor! Pois Deus está presente no meio dos justos. 6 Vocês, malfeitores, frustram os planos dos pobres, mas o refúgio deles é o Senhor. 7 Ah, se de Sião viesse a salvação para Israel! Quando o Senhor restaurar o seu povo, Jacó exultará! Israel se regozijará!
drop test simulation time|numerical drop test